Procesy realizowane wewnątrz hali magazynowej mają na celu efektywny przepływ dóbr w łańcuchu dostaw, jednak są obarczone wieloma zagrożeniami dla zdrowia i życia ludzkiego. By ograniczyć ryzyko do minimum, należy sumiennie przestrzegać norm i przepisów obowiązujących w miejscu pracy. Regulują one zarówno kwestie transportu wewnątrzzakładowego, w tym poruszanie się pieszych i operatorów obsługujących wózki widłowe, jak i stan nawierzchni ciągów komunikacyjnych. Wyznaczają również zasady składowania towarów, poruszają zagadnienia z zakresu dopuszczalnych odstępach między regałami w magazynie, a także ustalają zakresy szkoleń pracowników dotyczących standardów pracy w przedsiębiorstwie zgodne z założeniami przepisów BHP.
Dziś o odległościach, które powinny być zachowane pomiędzy regałami, dowiemy się czy jest to kwestia uregulowana prawnie. Następnie skupimy się na magazynie wysokiego składowania i sprawdzimy jak zmieni się szerokość korytarza roboczego przy zastosowaniu wózka widłowego Reach Truck oraz wózka systemowego. Zapraszamy.
Odległość między regałami w magazynie – przepisy bhp
Nadrzędnym aktem prawnym, z którego wynikają podstawowe przepisy dotyczące pracy w magazynie jest Rozporządzenie Ministra Pracy i Polityki Socjalnej z dnia 26 września 1997 r. w sprawie ogólnych przepisów bezpieczeństwa i higieny pracy.
Przepis § 69 traktuje o regałach, w 1 ust. ww. dokumentu czytamy, że „Regały powinny mieć odpowiednio wytrzymałą i stabilną konstrukcję oraz zabezpieczenia przed ich przewróceniem się.”, 2 ust. tego rozporządzenia głosi „Szerokość odstępów między regałami powinna być odpowiednia do stosowanych środków transportowych oraz powinna umożliwiać bezpieczne operowanie tymi środkami i ładunkami”. Dodatkowo, jeżeli powierzchnią pomiędzy regałami odbywa się transport, ma zastosowanie kolejny przepis ze wspomnianego rozporządzenia – § 4 ust. 2 „Drogi i przejścia powinny posiadać wymiary odpowiednie do liczby potencjalnych użytkowników oraz rodzajów i wielkości stosowanych urządzeń transportowych i przemieszczanych ładunków. Minimalne wymiary dróg i przejść określają Polskie Normy.”
W Polskiej Normie oznaczonej nr PN-M-78010:1968 „Transport wewnętrzny. Drogi i otwory drzwiowe. Wytyczne projektowania” wyszczególniono wskazówki na temat projektowania dróg transportowych w budynkach magazynowych. Ustalono m.in. że:
- dla silnikowych pojazdów transportowych poruszających się w ruchu jednostronnym (bez jednoczesnego ruchu pieszych i innych środków transportu) minimalna szerokość drogi na odcinkach prostych powinna wynosić:
B = a + 60 cm
Zmienna a to szerokość środka transportowego(gdy ładunek jest szerszy niż wózek przyjmuje się szerokość ładunku). Szerokość drogi (B) nie powinna być jednak mniejsza niż 120 cm.
- gdy pomiędzy regałami mogą poruszać się w tym samym czasie piesi, to szerokość (B) powinna wynosić co najmniej:
B = a + 100 cm
Czyli wózek widłowy wraz z ładunkiem, który może wystawać za obrys wózka plus 100 cm nie może być mniejszy niż 220 cm.
Warto wiedzieć, że stosowanie PN było w Polsce obowiązkowe do 1 stycznia 2003 r., teraz obowiązuje system normalizacji dobrowolnej. Przyjęło się jednak, że korzystanie z norm jest systemem bezpieczeństwa, a przedsiębiorcy posługujący się nimi są postrzegani jako wiarygodni i uczciwi partnerzy biznesowi.
Szerokość drogi dla wózka widłowego, a wysokie składowanie
Pojęcie wysokiego składowania towarów dotyczy magazynowania ich na wysokości od 7,2 m i powyżej, nawet do 50 m. Największą zaletą tego typu przechowywania jest bardzo duża pojemność przy jednoczesnej redukcji powierzchni działki pod zabudowę magazynową, czyli, prościej mówiąc, możliwość przechowywania znacznej ilości ładunków na jednym metrze kwadratowym. Wpływa to na optymalizację przestrzeni składowania, a to przekłada się na zmniejszenie kosztów eksploatacji danego obiektu.
Więcej na temat składowania przeczytasz tutaj.
Magazyn wysokiego składowania jest miejscem szczególnym, zatem także pojazdy z gamy urządzeń transportu bliskiego, które go obsługują, nie są standardowe. Pierwszym rodzajem jest wózek boczny typu Reach Truck – najbardziej popularny i uniwersalny sprzęt do obsługi niemal każdego systemu regałowego, nade wszystko przydatny w pracy z ładunkiem o wadze 1 400 – 2 000 kg, na wysokości ponad 13 m. Charakteryzuje się niskimi spadkami udźwigu, a dla aplikacji typu chłodnia lub mroźnia może zostać doposażony w kabinę do pracy w bardzo niskich temperaturach. Wózki wysokiego składowania są przeznaczone do pracy w wąskim korytarzu roboczym, którego szerokość najczęściej wynosi od 2 800 mm do 3 200 mm.
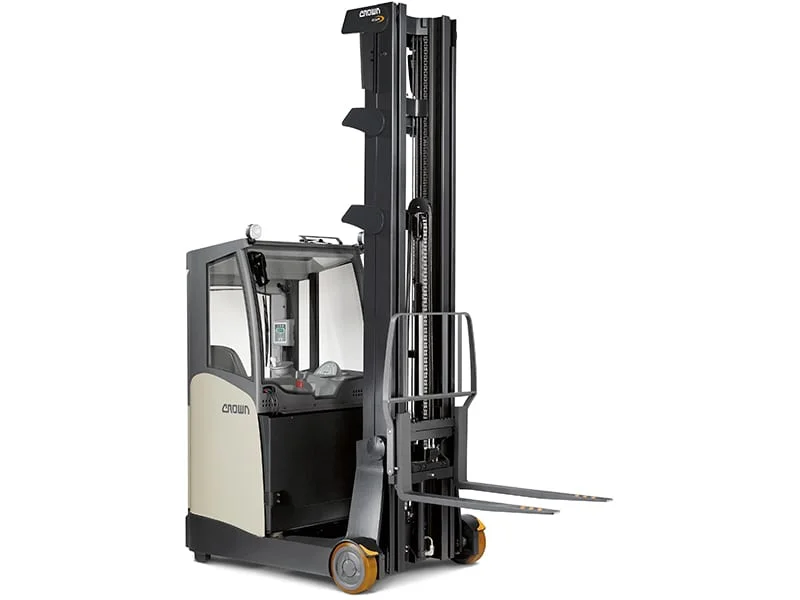
Kolejnym wózkiem do zadań specjalnych jest wózek systemowy VNA (ang. Verrry Narrow Aisles), z unoszącą się kabiną operatora. Pozwala na pracę z ładunkiem spaletyzowanym o wadze 1 000 – 1 500 kg, na wysokości do 17m. Dodatkowo ułatwia proces ręcznej kompletacji. Jego wzmocniony maszt eliminuje nieprzyjemne wrażenie operatora dotyczące kołysania ładunkiem. Dzięki wygodnej, opcjonalnej kabinie operator może działać w skrajnych temperaturach, czyli w chłodniach i mroźniach. To wyjątkowy wózek, przeznaczony do bardzo wąskich korytarzy roboczych, o szerokości wynoszącej zaledwie 1,65 – 1,80 m, co znacznie wpływa na wzrost współczynnika wykorzystania powierzchni magazynu.
Odległość pomiędzy regałami w magazynie – podsumowanie
Właściwa organizacja magazynu zakłada przede wszystkim bezpieczeństwo pracowników oraz ruch ładunków wykorzystujący najkrótszą drogę przy jak najmniejszym zużyciu środków transportu bliskiego. By zachować te warunki, konieczne jest zaprojektowanie miejsca przyjęcia, składowania, kompletacji i wydania ładunku w oparciu o dokładną analizę potrzeb danej firmy, a także rodzaju asortymentu z uwzględnieniem wyboru preferowanego systemu składowania oraz wózków widłowych, które będą go obsługiwać. Bardzo ważnym wskaźnikiem informującym o wydajności obiektu jest szerokość korytarza roboczego, zatem odległość pomiędzy regałami w magazynie. Uzyskanie jak najmniejszej przestrzeni jest pożądane, bo wiąże się z realnymi oszczędnościami – wpływa na zwiększenie powierzchni składowania i osiągalne przy użyciu wózków typu Reach Truck oraz bardziej zaawansowanych wózków VNA.
Dlaczego szerokość korytarza roboczego to ważny parametr? Więcej przeczytasz tu.